Projects
SIR Group Projects. Projects lead by the Service and Industrial Robotics group.
The robotics field-of-application is constantly growing as the technological advances allow new capabilities and an increment and strength of the already existing ones. Among the new applications, it is worth mentioning, due to their potential significance from the productive and social point of view, those in which the robots work jointly with the humans, originating the concept of “coworker robots”. In this type of applications, the robots require some special features. On the one hand, they must have certain level of autonomy and capacity of decision, as their role is no longer doing repetitive tasks in the classical way but on the contrary, they must adapt themselves with swiftness to changing conditions, especially to those produced by the humans in the same workspace. This adaptation implies an interaction with the human operators that constraint the robot movements and actions with the aim of avoiding potential injuries to humans, but without affecting the robot efficiency. In order for the coworker robots to be useful for the human operators, it is necessary that they have an important level of dexterity so that they can perform a number of different actions usually required in the human activities. In this context, the project aims for solutions that increment the performance of the coworker robots to allow their permanent establishment in our society, and, at the same time, facilitate their acceptance by the humans. With this aim, the project will deal with the topics mentioned above, developing algorithms and procedures that make easy the efficient cooperation between coworker robots and humans. Specifically, contributions are expected in relevant topics, as: the increment of the robot capability to autonomously manage the required tasks and the movements to execute them, using ontologies to represent the knowledge; the increment of the dexterous and bimanual manipulation capabilities, monitoring the movements to prevent potential failures; and the improvement of the interaction with the human operators regarding reactive, cooperative and exchange-objects movements, considering approaches based on demonstrations or on teleoperation. All the theoretical developments will be checked and validated experimentally using the systems specifically prepared for it in the project. Besides, as usual in the developments of the group, the mentioned problems will be addressed with the intention of providing general solutions, valid for both industrial and service robotics,taking care of the productive and social components.
]
El objeto del convenio es la realización de una aplicación robotizada que, en el ámbito de la edición del festival Primavera Sound 2018 a realizarse en las ciudades de Barcelona y Porto (Portugal), muestre un robot simulando realizar las tareas de un “disc-jockey”. Participantes: Aliakbar Akbari, Muhayyuddin, Mohammed Diab, Leopold Palomo.
Mobile manipulators with dexterous manipulation capabilities already exist and they can assist man in simple tasks in a versatile manner. In work environments its use as co-workers is possible, acting as logistic transporters and as versatile and dexterous manipulators, to cooperate with human operators to improve the efficiency of the work done. Nevertheless, to make this reality, some improvements in hardware and software are still required in order to allow a higher degree of adaptability. This project pursues a system composed of several mobile manipulators capable of acting in indoor semi-structured environments executing handling and assembly tasks in collaboration with human operators. The system must facilitate the human-robot collaboration that, on the one hand, can be done in an autonomous way (i.e. the mobile manipulators are required to cooperate with humans by performing autonomously complementary tasks while moving around in the humans environment and in their presence) and, on the other hand, can be done through interaction (i.e. with a virtual interaction via teleoperation, or with a physical interaction through an object jointly handled). The project focuses on the development of planning, reasoning and control algorithms, and in the development of the necessary software to provide mobile manipulators with the autonomy and the capacity of interaction to allow the cooperation with humans. In the sought horizon, robot co-workers must provide support to humans and integrate into their tasks and movements in a natural, fluid, safe and minimally invasive way, facilitating the acceptance by human workers of the changes that may result. Upon completion of the project, it will be available a test bed that should allow to investigate the behavior of humans in front of the work jointly carried out with robot co-workers, as well as the perceptions and the possible social acceptance of the changes involved. The project aims, therefore, to contribute to the resolution of the problem posed by the introduction of robots as co-workers, for the change that it may represent at the social level, and for its individual and collective perception, since the early consideration of these aspects will contribute to the acceptance of robots as an integral part of our lives and to its use without delay.
Related Links
In recent years there have been significant advances in the area of object grasping and manipulating using robots, both from the point of view of developing new mechanical hands with anthropomorphic structure as in terms of algorithms to search for an efficient use of these hands. However, the actual implementation of these hands in tasks that require some skill is still quite limited and it is still common the use of grippers specially designed for a certain application, and even the use of very simple grippers with only two opposite fingers when looking for usefulness and robustness. One of the main causes of this limitation is the difficulty in determining the appropriate movements to perform a task in the presence of several uncertainty sources, a problem that can be tackled by making greater use of tactile information in all the phases of the grasping and manipulation tasks. On the other hand, mobile robotics has also advanced significantly, to the point of defining its own work field with many different applications, but when the mobile device is provided with a device for grasping and dexterous manipulation they generally work in uncoupled way, the mobile device is positioned according to certain criteria and then the grasping device acts as an static one. In this context, the overall objective of the project is to advance towards the elimination of these deficiencies. The robotics group of the IOC has extensive experience in the area of grasping and manipulation objects with robotic hands, planning and optimizing the movements of both the hand and the arm that supports it, and now it is intended to extend that experience in two directions. Basically, on one hand, deepening in the problems concerning the use of dexterous hands with many degrees of freedom when there exist different sources of uncertainty, for which there will be special emphasis on the use of tactile information, and, on the other hand, addressing the problem of determining efficient actions when the whole dexterous manipulation device is mounted on a mobile element. As a complementary topic it is also considered the cooperative action of more than one manipulator. Thus, the project aims to make contributions in the three typical levels of these systems: hand level, arm level and body level. As in previous projects of the group, the above problems are addressed with the intention to provide general solutions that are valid both in industrial and service robotics.
Execution of a research and development project consisting of the viability analysis of a mark based method to determine system measurement error.
Related Links
- Luis Basañez's personal webpage
- Luis Basañez's staff record
- Financing entity:
Tecnomatrix BCN, SL
Among the current cutting-edge robotics topics, telerobotics occupies an outstanding position and many research centers around the world are spending a sustained effort in solving its problems. There are multiple reasons for such interest. Telerobotics is much more than the remote control of a robot, and today it is considered as an extension of the sensitive faculties and actions of humans. In this sense, its application areas are very extensive and range from medicine, surgery and space exploration to demining and construction of buildings and infrastructure. The communication capabilities offered by the Internet have decisively contributed to such development.
Many achievements have been reached in telerobotics, but there are still crucial issues to be solved. On one hand, new control algorithms that rigorously ensure the stability when operating in more demanding conditions such as variable delays, flexible joints, mobile manipulators and cooperative manipulation between robot-robot and human-robot. On the other hand, it is necessary to increase the aids to the operator, allowing for example, the interaction with the scene through the real 3D images and enabling in this way the effective use of tools such as relational positioning.
A natural extension of telerobotics is the teleoperation of robot networks, which has the problems of synchronization and consensus. These problems are attracting the attention of the scientific community due to their possible extension to other different fields than robotics, such as nonlinear systems described by Euler-Lagrange equations that cover a large number of physical systems of practical interest for which robots are a particular case.
The project aims to address the aforementioned issues through rigorous theoretical developments, simulations and real experiments in order to validate the results. In recent years, the research group has earned a leading international position among the most advanced telerobotics groups, and it is well placed for making significant contributions as the result of the development of the proposed project. These contributions may be applied to both industrial and service robotics, which make use of both fixed and mobile manipulators as well as humanoid robots.
The majority of robotized tasks, as well as those of potential robotization, whether in industrial or service robotics, require adequate grasping and manipulation of objects. This fact, together with advances in the design, construction and control of electromechanical systems, has led to the development of sophisticated and versatile grasping elements, including the proposal of anthropomorphic mechanical hands, some of which are already commercially available. The complexity of the tasks to be carried out by such devices has given rise to a line of research oriented to solving automatically the problems of grasping and manipulation. The objective is essentially to hold and manipulate an object in an optimal fashion for a given purpose; as a function of the case, this may involve a number of associated problems, such as determining adequate contact points on the object, appropriate hand configurations, correct grasping forces, and collision-free trajectories for hand and robot, among other related problems, always characterised by a high computational complexity. Considerable progress has been achieved along this line of research, including contributions of the proposing group in the course of previous research projects. But there is still a long way to go and the current challenge is to advance a qualitative step in the robotized grasping and manipulation of objects by developing the algorithms needed to automate multi-hand systems, i.e. when more than one grasping element is available. The object of the present project is to achieve this qualitative jump, by proposing new techniques and developing new algorithms that allow multi-hand systems to perform those tasks, both for cases that require more than one grasping element and for those that, though not absolutely required, the use of more than one grasping element allows better solutions based on different optimisation criteria (for instance, more robustness or adaptability to the task). In the framework of the project a two-hand system will be implemented and used to validate experimentally the theoretical developments. The results of the project could be applied both in industrial environments and in service robotics; moreover, they are foreseeing to be essential for the efficient use of humanoid robots, which obviously need to be capable of resolving tasks with their two hands in a similar fashion to human beings.
The aim of the project is to develop a surgical robotic manipulator device focused on the improvement of surgical interventions with anastomosis. These interventions consist basically in doing a cross-cutting of a tubular tissue (usually the intestine) removing a piece of it and uniting again the resulting ends. This is a common procedure in the treatment of cancer of colon, which has big incidence in occidental population. Nowadays, the union of the two extremes of intestine can be done by two different ways:
- With manual suture, where the surgeon sews with special yarn and needle the ends of the intestine in a complex and long procedure.
- Using a surgical stapler (special mechanic device) that unites the two extremes with metallic staples.
The main disadvantages of these methods respectively are:
- The hand suture is really difficult (needs highly skilled surgeon) and is slow, increasing significantly the infection risk.
- The metallic staples are not absorbed by the organism, creating a ring in the intestine with poor elasticity, really below the rest of intestinal tissue, so this can create obstructions that can appear during the rest of the life of the patient. On the other hand, the stapler device is inserted by the closest open-end of the intestine and is rigid, so it has reduced accessibility to many parts of the intestine.
The objective of this project is to develop a manipulator device to unite the two extremes of the intestine by means of a sewing with absorbable yarn, doing it fast, automatically and in a robust way, under supervision of the surgeon. Thus, improving the quality of life of the patient and reducing the risks associated to the surgery intervention. This device will avoid the disadvantages of the existing methods: it will do a fast sewing suture with yarn that can be absorbed again by the organism, thus keeping the affected zone elastic after the intervention. This will avoid obstruction problems and also will improve the regeneration of the tissues in the sewed zone. The sewing task must be done in a problematic environment, with non-regular tissues and changing properties due to muscle effects and viscosity of the material itself. This will made necessary the application of sensors and advance control over the actuators in order to making the device capable to sew the tissues in reliable way.
The project is carried out by two Research Institutes of the UPC, the IOC and the INTEXTER, highly skilled in robotics and sewing technology respectively, and an important hospital with high expertise in the related surgery intervention.
The anastomosis procedure is used in the surgery for treatment of different diseases (like Crohn’s, polyps or diverticulitis), but the most common is the cancer of colon. It is important to highlight the high incidence of this kind of cancer in the world population. The colorectal cancer is the third most common cancer in European men (after lung and prostate cancers) and the second in women (after breast cancer). This cancer is the second cause of death by cancer in men, behind of the of lung cancer, and behind the breast cancer in women. It is expected that this innovative new surgical device technology will contribute significantly to increase the life expectancy of the population. The success of the study, development and implementation of the new sewing robot, will produce a very positive social impact, not only for patients, also for the national Health Departments. It is intended to achieve better results for the patient, than with the techniques used today, in the evolution of his disease and in the quality of life after the intervention. The patient will not have all the common complications anastomosis interventions like staples rejection by the body and bowel or dehiscence. This reduction of post procedural complications means a reduction of time staying in hospital, and it not only translates into a better and more prompt recovery of the patients, it also means a lower cost for the Health Department.
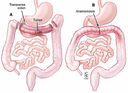
Related Links
- Dr. Raúl Suárez's personal webpage
- Dr. Raúl Suárez's staff record
- José Antonio's personal webpage
- Financing entity:
Commission of European Communities - Participating entities:
- Link to entry on university database
- QR
The global objective of this project is the study, the implementation and the evaluation of guided systems to aid the execution of bronchoscopies for the examination of peripheral lung lesions. The project is organized in two subprojects, a development subproject and an evaluation one. The development subproject (GUIBROe) is going to be carried out at the Institute of Industrial and Control Engineering at the Universitat Politècnica de Catalunya. The evaluation subproject (GUIBROe) is going to be carried out at the Hospital Universitari de Bellvitge and at the Hospital del Mar.
In the present subproject we first propose the implementation of a virtual bronchoscopy system with an automatic trajectory generation engine to allow the virtual guiding using a haptic device. This system will resolve the intrinsic problems found when searching for 3D paths using 2D information from the computerized tomography. It will allow as well the virtual performance of the bronchoscopy previously to the execution of the real one. The navigation in the virtual model will be performed using a haptic device that will constrain the motions to the computed path using force feedback. In this sense the proposed system will be a useful learning tool, too.
An assisted bronchoscopy guided system is also proposed to guide the doctor during the execution of the bronchoscopy by using augmented reality data superimposed to the real video (the virtual model can even be superimposed to the image if its quality is low). The proposed system will indicate the solution path and the motions to be done to follow it.
The methodology to carry out the project is based on an incremental implementation that permits to check the correctness of the system with increasing functionalities, and allow the doctors of the associated subproject GUIBROe to evaluate it.
The goal of this project is the generation of knowledge and the development of techniques aimed at the remote execution of robotized tasks commanded by one or more operators and carried out by multiple robots cooperating in a network, making use of the possibilities of Internet2 and of haptic devices.
This proposal claims to be a significant step forward in this topic, by overtaking the classic teleoperation between local and remote stations and the master/slave approach. The project proposes a set of multifunctional stations, whose role depends on the specific task to be performed and where the different robots execute cooperative tasks telecommanded by one or several operators.
The concept of networked cooperative teletasking gathers several tools and disciplines like coordinated control with time delay, relational positioning based on geometric constraints, real and virtual force feedback, guidance by virtual reduction of degrees of freedom, augmented reality and Internet or Internet2, that can give new prospects to the remote use of robots in industrial and service applications.
This project counts on the support and advice of several industrial companies, and especially with the I2CAT Foundation, whose collaboration is essential for the development and experimentation with Internet2.
Besides its fundamental purpose of incrementing scientific and technical knowledge, the project envisages a medium-term real-life applicability horizon of its results.
Related Links
- Luis Basañez's personal webpage
- Luis Basañez's staff record
- Financing entities:
- Secretariat of state for science and innovation
- European Union [ERDF]
- Link to entry on university database
- QR
En el estadio actual de la robótica uno de los problemas que aún requiere mejoras sustanciales es la realización de acciones de prensión y reposicionamiento de objetos con suficiente destreza y seguridad. En entornos industriales sumamente estructurados esta problemática se minimiza recurriendo a pinzas muy específicas y de funcionamiento simple, que como contrapartida tienen muy poca versatilidad; pero en numerosas aplicaciones, y muy especialmente en la robótica de servicios actualmente en auge, el problema dista de estar satisfactoriamente resuelto y significa una gran limitación. Dado que es necesario trabajar con una variedad de objetos notable, la necesidad de pinzas versátiles resulta entonces evidente y el problema pasa a ser cómo programar y llevar a cabo las tareas de prensión y manipulación diestra de objetos de forma autónoma. Aunque con ciertas limitaciones, ya existen propuestas para realizar prensiones precisas de un objeto (el propio grupo de trabajo ya ha contribuido en esta línea en proyectos anteriores), pero el problema de sujetar, manipular y reposicionar un objeto mediante el movimiento de la mano está aún muy abierto. En este marco, el objetivo del proyecto consiste en proponer nuevos enfoques y desarrollar nuevos algoritmos para llevar a cabo la prensión y el posterior reposicionado de un objeto utilizando el movimientos de los dedos, tal como lo hace el ser humano, por lo que se pone énfasis en la utilización de un elemento prensor antropomorfo, y en la utilización de técnicas que permitan extraer de la experiencia humana la información necesaria para replicar las tareas mediante un robot equipado con una mano mecánica diestra.
The goal of this project is to generate knowledge and to develop techniques aimed at the remote operation of multirobot systems for industrial applications, in order to obtain a comprehensive system of aided teleoperation.
This proposal claims to be a significant step forward in the remote tuning and supervision of industrial robot tasks, grouping several tools and disciplines around teleoperation, like relational positioning based on geometric constraints, real and virtual force feedback, guidance by virtual reduction of degrees of freedom, augmented reality and Internet2 communication.
The combination of these disciplines can give a new dimension not only to remotely operated multirobot systems in industrial tasks, but also in other fields like the social, sanitary and aerospace domains. In particular, the use of relational positioning and Internet2 is quite new in this area.
This project counts on the support and advice of several industrial companies, and especially with that of the I2CAT Foundation, whose collaboration is essential for the development and experimentation with Internet2.
Besides its fundamental purpose of scientific and technical knowledge progress, the project envisages a medium-term real-life applicability horizon of its results.
The main goal of the project is the development of algorithms and techniques for the automatic programming, tuning and supervision of industrial tasks performed by robotized cells, making use of the facilities provided by Internet and the haptic devices. In principle the project basically considers assembly and polishing tasks but the results could be easily transferred to other industrial tasks that can be performed by robots, like cutting and material disposing.
This proposal claims to be a significant forward step over the results of a previous project, bugged by the CICYT, where an aided programming system to make easier the use of robotic cells for industrial tasks like the above mentioned has been developed. The new project will also try to make relevant contributions in other aspects that are essential for the success of a robotized industrial application: task tuning and task execution supervision. The project will explore the possibility of performing both aspects in a remote way from the operations room where the cell programming takes place, and all this minimizing the presence of human operators at the cell.
To achieve these goals, the project will develop a set of modules addressed to allow the teleoperation of the cell's robots through Internet (in the close future, Internet 2) making use of visual, acoustic and force feedback, the last one handled by the same haptic device also used for task programming.
The objective of the project is the development of a semi-automatic system to assist the programming of robotic cells in industrial tasks where there is physical interaction between the robot end effector or the manipulated object and another objects in the workspace, like, for instance, cutting, deburring, polishing, and assembling. The communication between the human operator and the programming system will be based on two basic components: the graphic representation of the objects and the robotic cell, and the interaction with them through a virtual touch device.
The goal of the project is to contribute to solve one of the major obstacles found in the application of robots in certain industrial tasks: the complexity and cost of the robot programming. This problem is specially critic for the tasks tackled in this project, whose complexity is due to the need of using sensorial information, to the difficulty of controlling contact movements, and to the importance of the different uncertainties affecting the task as well as the object tolerances. For this type of tasks, the project proposes a new programming approach based on the use of virtual touch.
Related Links
- Luis Basañez's personal webpage
- Luis Basañez's staff record
- Financing entity:
Interministerial Commission for Science and Technology (CICYT) - Link to entry on university database
- QR
The polishing and finishing of metallic parts are fundamental operations in numerous industrial manufacturing fields. Presently, these operations are usually performed manually by specialised companies. This implies low productivity and high social cost since these operations are very tiring for workers. Industrial robots are effective tools for the automation of polishing operations and many research centres in advanced countries are studying their utilisation.
This project deals with the development of a set of techniques and methods leading to the total automation of the programming task of a polishing robotized cell and of the execution of the phases that make up the process: parts location, grasping, polishing operations and finish quality control.
Related Links
- Luis Basañez's personal webpage
- Luis Basañez's staff record
- Financing entity:
Interministerial Commission for Science and Technology (CICYT) - Link to entry on university database
- QR
Share: